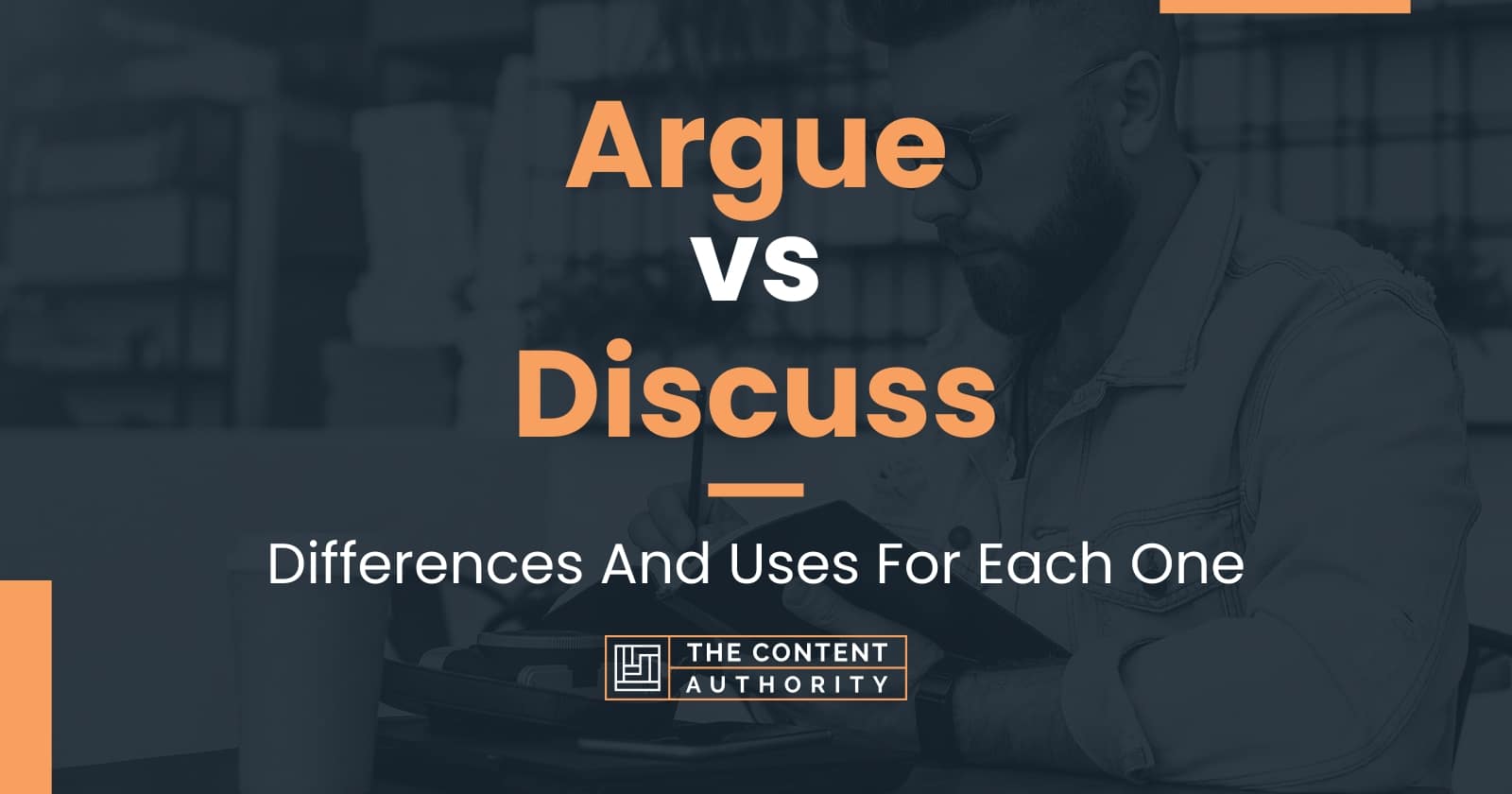
Обо мне
How to Calculate Factor of Safety: A Clear GuideCalculating the factor of safety is an essential step in engineering design to ensure that the structure or component can withstand the expected loads without failure. The factor of safety is the ratio of the maximum strength of the structure or component to the design load it is expected to support. If the factor of safety is less than 1, it means that the structure or component cannot support the design load, and it is likely to fail. Therefore, it is crucial to calculate the factor of safety accurately to ensure the safety and reliability of the structure or component.
The factor of safety is used in various fields, including civil, mechanical, electrical, and aerospace engineering, to ensure that the design meets the required safety standards. The factor of safety takes into account the uncertainties in the loads, material properties, and other factors that can affect the performance of the structure or component. Therefore, it is essential to consider all the relevant factors and use appropriate methods to calculate the factor of safety accurately.
In this article, we will discuss the different methods used to calculate the factor of safety and provide examples of how to apply them in practical engineering design. We will also discuss the importance of the factor of safety in ensuring the safety and reliability of the structure or component and how it can be used to optimize the design for cost and performance. By the end of this article, you will have a clear understanding of how to calculate the factor of safety and its importance in engineering design.Understanding Factor of Safety
Definition and Significance
A factor of safety (FoS) is a numerical value that represents the safety margin built into a design or system. It is defined as the ratio of the maximum load or stress a component can withstand to the maximum load or stress it is expected to experience during normal operation. The FoS is a measure of the reliability and safety of a design, and it is used to ensure that the design can withstand unexpected loads or stresses without failing.
The FoS is a critical factor in engineering design, particularly in civil, mechanical, and aerospace engineering. It is used to ensure that structures, machines, and systems are designed to be safe and reliable. For example, in civil engineering, the FoS is used to ensure that buildings, bridges, and other structures can withstand the loads and stresses they are expected to experience during their lifetime. In mechanical engineering, the FoS is used to ensure that machines and equipment can operate safely and reliably under normal and unexpected conditions.
Historical Context
The concept of FoS has been used in engineering design for centuries. The ancient Greeks and Romans used FoS in their designs of aqueducts, bridges, and other structures. In the 17th century, Galileo Galilei introduced the concept of FoS in his work on the strength of materials. In the 19th century, engineers began to use FoS more systematically in their designs, particularly in the design of steam engines and locomotives.
Today, FoS is an essential part of engineering design and is used in a wide range of applications. It is used to ensure the safety and reliability of everything from airplanes and automobiles to buildings and bridges. Engineers use sophisticated computer models and simulations to calculate the FoS of complex systems and designs, and they use this information to refine their designs and ensure that they are safe and reliable.
In summary, the FoS is a critical factor in engineering design, and it is used to ensure that structures, machines, and systems are safe and reliable. The concept of FoS has been used in engineering design for centuries, and it continues to be an essential part of modern engineering design.Fundamentals of Calculation
Determining Load and Stress
Before calculating the factor of safety, it is essential to determine the load and stress that the structure or component will experience. The load can be defined as the force acting on the structure or component, while stress is the force per unit area. Stress can be calculated by dividing the load by the cross-sectional area of the structure or component.
Material Strength Parameters
The next step in calculating the factor of safety is to determine the material strength parameters. These parameters include the ultimate strength, yield strength, and elastic modulus of the material. The ultimate strength is the maximum stress that the material can withstand before it fails. The yield strength is the stress at which the material starts to deform plastically. The elastic modulus is a measure of the material's stiffness.
Safety Factors for Various Materials
Different materials have different safety factors due to variations in their strength and reliability. For example, the safety factor for steel is typically 1.5, while for aluminum, it is 1.2. For brittle materials such as ceramics, the safety factor is much higher, typically around 10. It is essential to use the appropriate safety factor for the material being used to ensure the safety and reliability of the structure or component.
In summary, calculating the factor of safety involves determining the load and stress, determining the material strength parameters, and using the appropriate safety factor for the material. By following these steps, engineers can ensure that structures and components are designed to be safe and reliable.Types of Factor of Safety
Yield, Ultimate, and Allowable Stress
The factor of safety is calculated based on different types of stresses. The most common types of stresses used in the calculation of factor of safety are yield stress, ultimate stress, and allowable stress. Yield stress is the stress at which a material begins to deform plastically. Ultimate stress is the maximum stress a material can withstand before it fractures. Allowable stress is the maximum stress a material can withstand without causing permanent deformation.
The factor of safety for yield stress is calculated as the ratio of yield stress to working stress. Similarly, the factor of safety for ultimate stress is calculated as the ratio of ultimate stress to working stress. The factor of safety for allowable stress is calculated as the ratio of allowable stress to working stress.
Static and Dynamic Loading Conditions
The factor of safety is also calculated based on the type of loading condition. Static loading conditions are those where the load is applied gradually and the material is allowed to adjust to the load. Dynamic loading conditions are those where the load is applied suddenly and the material does not have time to adjust to the load.
The factor of safety for static loading conditions is calculated based on the maximum stress the material can withstand. The factor of safety for dynamic loading conditions is calculated based on the maximum stress the material can withstand multiplied by a dynamic factor.
In summary, the factor of safety is calculated based on the type of stress and loading condition. The yield stress, ultimate stress, and allowable stress are the most common types of stresses used in the calculation of factor of safety. Static and dynamic loading conditions are the two types of loading conditions used in the calculation of factor of safety.Calculating Factor of Safety
Formula and Computation
The factor of safety is a ratio that quantifies the safety level and reliability of a structure or component. It is defined as the ratio of the ultimate stress of the component material to the working stress . The formula for calculating the factor of safety is:
Factor of Safety = Ultimate Stress / Working Stress
Where Ultimate Stress is the maximum stress that a material can withstand before it fails, and Working Stress is the stress that the material is subjected to during normal operation.
To calculate the factor of safety, one needs to determine the ultimate and working stresses of the material. This can be done by conducting material tests or consulting material data sheets. Once these values are known, the factor of safety can be computed using the formula above.
Example Calculations
For example, consider a steel beam that is subjected to a maximum load of 10,000 N. The working stress of the beam is 50 MPa, and the ultimate stress of the steel is 400 MPa .
To calculate the factor of safety, the ultimate stress needs to be divided by the working stress:
Factor of Safety = Ultimate Stress / Working Stress
= 400 MPa / 50 MPa
= 8
In this case, the factor of safety is 8, which means that the beam can withstand a load that is 8 times greater than the maximum load it is subjected to during normal operation.
Another example is a bridge that is designed to support a maximum load of 100,000 kg. The working stress of the bridge material is 20 MPa, and the ultimate stress is 200 MPa .
The factor of safety can be calculated as follows:
Factor of Safety = Ultimate Stress / Working Stress
= 200 MPa / 20 MPa
= 10
In this case, the factor of safety is 10, which means that the bridge can withstand a load that is 10 times greater than the maximum load it is designed to support.
In summary, the factor of safety is an important metric that helps ensure the safety and reliability of structures and components. By calculating the factor of safety, engineers can determine whether a structure or component is safe for its intended use.
Footnotes
Factor of Safety: Definition, Equation, Examples, Calculator
Factors of Safety - FOS - The Engineering ToolBox
Factor of Safety Calculator - CalcTool
Applications in Engineering Design
Design for Structural Integrity
Factor of Safety (FoS) plays a crucial role in designing structures that can withstand various loads and stresses. It is used to determine the strength of materials and to ensure that the structure is safe and reliable. Engineers use FoS to design structures such as buildings, bridges, and dams that can withstand natural disasters like earthquakes, hurricanes, and floods.
For example, in the design of a building, engineers must consider the maximum load that the structure can withstand before it collapses. They use FoS to ensure that the building can withstand the maximum load without collapsing. The FoS value depends on the material used, the design of the structure, and the type of load it will be subjected to.
Design for Mechanical Components
FoS is also used in the design of mechanical components such as gears, shafts, and bearings. It is used to ensure that the components can withstand the loads and stresses that they will be subjected to during operation. Engineers use FoS to determine the strength of the material and to ensure that the component will not fail during operation.
For example, in the design of a gear, engineers must consider the maximum torque that the gear can withstand before it fails. They use FoS to ensure that the gear can withstand the maximum torque without failing. The FoS value depends on the material used, the design of the gear, and the type of load it will be subjected to.
In conclusion, FoS is a critical factor in engineering design. It is used to ensure that structures and components are safe and reliable. Engineers use FoS to design structures and components that can withstand various loads and stresses. By using FoS, engineers can ensure that their designs are safe and reliable, and can withstand the test of time.Industry Standards and Guidelines
Building Codes and Regulations
Building codes and regulations are put in place to ensure that structures are designed and constructed to meet minimum safety standards. These codes and regulations are set by governmental agencies and are enforced by local building departments. The codes and regulations vary by location and building type, but they all have the same goal of ensuring public safety.
One of the key factors in building design is the factor of safety. The factor of safety is the ratio of the maximum load a structure can support to the maximum load it is expected to support. Building codes and regulations typically specify the minimum factor of safety required for different types of structures.
For example, the International Building Code (IBC) requires a minimum factor of safety of 1.5 for most structures. However, the factor of safety required for certain structures, such as bridges and high-rise buildings, may be higher. The IBC also requires that the factor of safety be calculated using the most critical load conditions.
Industry-Specific Safety Requirements
In addition to building codes and regulations, many industries have their own safety requirements. These requirements are often more stringent than the minimum requirements set by building codes and regulations.
For example, the Occupational Safety and Health Administration (OSHA) has specific requirements for fall protection systems in the construction industry. These requirements include a minimum factor of safety of 2 for personal fall arrest systems.
Other industries, such as aviation and transportation, also have their own safety requirements. These requirements may include factors of safety for equipment and structures, as well as for operational procedures.
It is important for designers and engineers to be aware of both building codes and regulations and industry-specific safety requirements when designing structures and equipment. By following these requirements, they can ensure that their designs are safe and meet the necessary standards.Assessing and Managing Risks
Risk Assessment Techniques
Before calculating the factor of safety, it is important to assess and manage risks. Risk assessment is the process of identifying potential hazards, analyzing and evaluating the risks associated with those hazards, and determining appropriate ways to eliminate or control those risks. There are several techniques for conducting risk assessment, including:
Qualitative Risk Assessment: This technique involves assessing risks based on subjective criteria such as likelihood and impact. It is a simple and cost-effective way to identify and prioritize risks but may lack accuracy and precision.
Quantitative Risk Assessment: This technique involves assessing risks using numerical data and statistical methods. It provides a more objective and precise way to identify and prioritize risks but may require more resources and expertise.
Fault Tree Analysis: This technique involves identifying all the possible causes of a hazard and analyzing their relationships to determine the likelihood of the hazard occurring. It is a useful technique for identifying the root causes of complex hazards.
Incorporating Factor of Safety in Risk Management
The factor of safety is an important concept in risk management. It is a measure of how much stronger a structure or system is than it needs to be to perform its intended function safely. Incorporating the factor of safety in risk management involves:
Identifying Critical Components: Identify the critical components of the structure or system that are most likely to fail or cause harm in the event of a hazard.
Determining Design Requirements: Determine the design requirements for the critical components based on the intended function and the potential hazards they may face.
Calculating Factor of Safety: Calculate the factor of safety for the critical components based on the design requirements and the maximum load or stress they may face.
Monitoring and Maintenance: Monitor the critical components and perform regular maintenance to ensure they continue to meet the design requirements and the factor of safety.
By incorporating the factor of safety in risk management, organizations can ensure that their structures and systems are designed and maintained to withstand potential hazards and minimize the risks associated with those hazards.Limitations and Considerations
Factors Affecting Safety Margins
When calculating the factor of safety, it is important to consider several factors that can affect the safety margins. These factors include the properties of the material used, the loads that the structure will be subjected to, and the accuracy of the analysis methods used. For instance, ductile materials such as steel can absorb more energy before failing compared to brittle materials such as ceramics. Therefore, the factor of safety for a structure made of steel will be lower than that for a structure made of ceramics.
Another factor to consider is the loads that the structure will be subjected to. Different loads such as wind, snow, and earthquake can have different effects on the structure. It is important to account for all these loads when calculating the factor of safety. Additionally, the accuracy of the analysis methods used can also affect the safety margins. For instance, if the analysis assumes a uniform distribution of loads when in reality they are not, the factor of safety may be overestimated.
Balancing Cost and Safety
While safety is a critical consideration when designing a structure, it is not the only consideration. Cost is also an important factor to consider. In some cases, increasing the factor of safety may significantly increase the cost of the project without a proportional increase in safety. Therefore, it is important to strike a balance between cost and safety.
One way to achieve this balance is by using the appropriate safety factor for the specific application. For instance, a safety factor of 1.5 may be appropriate for a structure that will be used for a short period, while a safety factor of 2.5 may be appropriate for a structure that will be used for a longer period. Additionally, it is important to consider the consequences of failure when determining the appropriate safety factor. For instance, a structure that will be used to transport hazardous materials may require a higher safety factor compared to a structure that will not.
In conclusion, calculating the factor of safety is an important consideration when designing a structure. It is important to consider the various factors that can affect the safety margins and strike a balance between cost and safety.Advancements and Future Directions
Technological Impact on Safety Calculations
The advent of computer-aided engineering tools has revolutionized the way engineers calculate factor of safety. These tools allow for more accurate and efficient calculations, reducing the risk of human error. Additionally, the use of simulation software has made it possible to test structures and machinery in virtual environments before they are built, further increasing safety.
Furthermore, the use of artificial intelligence (AI) in safety calculations is a promising area of research. AI algorithms can analyze vast amounts of data and identify potential safety hazards that may have been overlooked by humans. This technology can also predict the behavior of structures and machinery under different conditions, allowing engineers to design safer systems.
Trends in Material Science
The development of new materials has also had a significant impact on safety calculations. For example, the use of composite materials in aerospace and automotive industries has led to lighter and more fuel-efficient vehicles, but also raised concerns about their safety. Therefore, researchers are working to develop new materials that are both lightweight and strong, while also considering their environmental impact.
Another trend in material science is the use of smart materials that can change their properties in response to external stimuli. These materials have the potential to improve the safety of structures and machinery by automatically adjusting to changing conditions. For example, smart materials could be used in bridges that can detect and repair cracks before they become a safety hazard.
In conclusion, the advancements in computer-aided engineering tools, the use of AI in safety calculations, and the development of new materials are all promising areas for future research in factor of safety calculations. As technology continues to evolve, engineers will have access to more accurate and efficient tools to design safer structures and machinery.Frequently Asked Questions
What are the steps to determine the factor of safety in construction projects?
To determine the factor of safety in construction projects, engineers must first identify the loads that the structure will be subjected to during its expected lifetime. Next, they must determine the strength of the materials being used and the likelihood of failure. The factor of safety is then calculated by dividing the ultimate strength of the material by the maximum expected load.
Can you explain the process for calculating the safety factor in machine design?
The process for calculating the safety factor in machine design begins with identifying the loads that the machine will be subjected to during its expected lifetime. Next, engineers must determine the strength of the materials being used and the likelihood of failure. The safety factor is then calculated by dividing the ultimate strength of the material by the maximum expected load.
How do you determine the safety factor for lifting operations?
To determine the safety factor for lifting operations, engineers must first identify the weight of the load being lifted and the capacity of the lifting equipment. The safety factor is then calculated by dividing the capacity of the lifting equipment by the weight of the load. A safety factor of at least 5:1 is recommended for lifting operations.
What does a 5 to 1 safety factor imply in engineering terms?
In engineering terms, a 5 to 1 safety factor implies that the maximum load that a structure or component is designed to support is only 1/5 of the load that would cause it to fail. This means that the structure or component has a significant margin of safety and is unlikely to fail even under extreme conditions.
In what way can SOLIDWORKS be used to calculate the factor of safety?
SOLIDWORKS is a computer-aided design (CAD) software that can be used to calculate the factor of safety for 3D models. The software allows engineers to simulate the loads that a structure or component will be subjected to and determine the factor of safety based on the material properties and design specifications.
How is the total factor of safety computed in engineering analysis?
The total factor of safety in engineering analysis is computed by multiplying the individual factors of safety for each component of a structure or machine. For example, if a machine has three components with individual factors of safety of 2, 3, and 4, the total factor of safety would be 2 x 3 x 4 = 24.
Местоположение
Род деятельности